What do I need to pay attention to when installing and adjusting the grinding wheel?
Release time:
2024-06-01
Grinding wheel is a common grinding tool widely used in metalworking, welding, cutting and grinding processes.
Grinding wheel is a common grinding tool widely used in metalworking, welding, cutting and grinding processes. It is composed of abrasive particles and binder. The abrasive particles can be alumina, silicon carbide and other materials with high hardness, and the binder can be ceramics, resins and so on. When the grinding wheel is working, the abrasive particles are in contact with the surface of the workpiece, and the material on the surface of the workpiece is removed or changed in shape through friction and grinding action.
With the continuous development of product technology, the requirements for machining accuracy and surface integrity of the required parts are gradually increasing. For example, for the hydraulic system in the precision spool and valve sleeve, laser gyro plane reflector, video head, DVD player, etc., these have prompted the grinding process gradually toward the ultra-precision grinding, ultra-precision grinding, ultra-precision polishing direction.
In actual use, the installation of the grinding wheel needs to pay attention to a lot of things, such as: before clamping the grinding wheel should be lifted by the rope, and gently hit the grinding wheel for sound check. The sound should be crisp, no chatter or murmur; grinding wheel is usually installed using a flange, the two flanges selected should be the same diameter, to avoid the wheel rupture due to bending stress, the minimum diameter of the flange at least one-third of the diameter of the wheel, if there is no protective cover should be at least two-thirds of the diameter of the wheel;
When the grinding wheel is installed, between it and the flange, it is necessary to ensure a certain contact surface and uniform force by putting rubber, felt and other elastic gaskets. After the grinding wheel is installed, it should be air-run for at least 5 minutes to confirm that there is no problem before normal use and work;
If a new grinding wheel is installed, cracks, scars and other defects also need to be carefully checked before installation. And before and after installation, respectively, a balance adjustment, grinding wheel clamping is completed, after static balance, so that it is at the highest speed test rotation for 5 minutes, no anomalies before formal use;
Wheel static balance adjustment is usually done manually, and the tools needed are: balance frame, balance mandrel and balance block, level meter and so on. The operation needs to find out the lowest position point of the center of gravity of the grinding wheel, marked as A; and the corresponding point on the same diameter of the A point, marked as B; and then gradually add the balancing block C, and then add the balancing block D and E, during the period to ensure that the position of the A point and the B point remains unchanged;
In the event of a change in position, the wheel can be balanced by adjusting the balancing blocks D and E up and down to restore their position; thereafter turn the wheel by 90 degrees. In the same way to ensure that the position of point A. B. Finally, repeated adjustments to confirm that the wheel is stable in all directions, it means that the wheel has been balanced; usually need to check 6 or 8 directions.
Key words:
Grinding tools and abrasives
Previous
Next
Previous:
Next:
Related News
Address: No. 1-6, North Road, 50 m west of the intersection of Industrial Avenue and Pingshun Road, Xiping County, Zhumadian City, Henan Province
Telephone:+8613979353005
View Mobile
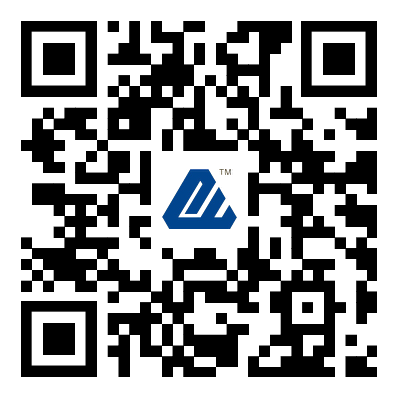