Adjustment and optimization of grinding wheel cutting parameters, how to make a reasonable choice according to the workpiece material?
Release time:
2024-06-04
As a core tool in grinding processing, the selection of grinding wheel directly affects the processing quality,
I. Introduction
As a core tool in grinding processing, the selection of grinding wheel directly affects the processing quality, efficiency and cost. Therefore, when selecting grinding wheels, a number of factors need to be considered comprehensively, including the characteristics of the workpiece to be processed, the performance of the grinding wheel abrasive and other important factors. This article will elaborate on these factors, aiming to help readers make more reasonable, more accurate grinding wheel selection decision.
Second, the workpiece to be processed
Material and hardness
Different materials of the workpiece on the grinding wheel requirements are different, such as steel, non-ferrous metals, non-metals, etc..
The hardness of the material directly affects the grinding wheel wear rate and grinding efficiency. Therefore, it is necessary to choose the appropriate grinding wheel formula and type according to the hardness and other characteristics of the material.
Processing part and shape
Consider the machining part of the workpiece, such as flat surface, external circle, internal circle, curved surface and so on.
The shape of the workpiece determines the suitability of the grinding wheel and the grinding method. For conventional shapes, such as internal holes, external circles, and flat surfaces, choose sintered or electroplated grinding wheels. For workpieces with complex shapes, plated grinding wheels are usually preferred because they are better adapted to complex shapes.
Grinding allowance
The size of the grinding allowance determines the degree of wear of the grinding wheel and the grinding time.
Select the appropriate type of grinding wheel and grit size according to the grinding allowance. When the grinding allowance is large, a coarse grit grinding wheel should be selected to improve the grinding efficiency.
Machining precision and finish requirements
Workpieces requiring high machining accuracy require the selection of high-precision grinding wheels.
Finish requirements affect the selection of grinding wheels. Coarse grit grinding wheels are suitable for workpieces with large grinding allowances, but may not be able to meet high finish requirements. At this time, the need to use a finer-grained grinding wheel for multi-process grinding to achieve the required finish.
Grinding Wheels
Shape and specification
According to the processing needs to choose the appropriate shape of the grinding wheel, such as flat, beveled edge, cup-shaped, etc..
Specification should consider the diameter of the grinding wheel, thickness, aperture and other parameters to ensure that the matching of the grinding wheel and processing equipment.
Grain size and hardness
Grain size determines the size of the abrasive grains on the surface of the grinding wheel, affecting grinding efficiency and surface quality.
The hardness of the grinding wheel determines the degree of consolidation and self-sharpening of the abrasive grains, thus affecting the durability of the wheel.
Type of bond
According to the processing needs and grinding wheel performance requirements to choose the appropriate type of bond, such as metal, resin, ceramic, etc..
Current equipment and processing method
Consider the power, speed and grinding method of the existing equipment and select the grinding wheel that matches it.
Select the appropriate type and material of grinding wheel according to the processing method (e.g. dry grinding, wet grinding). For example, wet grinding may need to choose a better water resistance of the grinding wheel.
Other Important Factors
Safety
Select grinding wheels that meet safety standards to ensure safety during processing.
Pay attention to the maximum working speed and balance requirements of the grinding wheel to prevent rupture or vibration of the grinding wheel when rotating at high speed.
Economic Considerations
Select a cost-effective grinding wheel based on processing costs and grinding wheel life.
Consider the replacement cycle of the grinding wheel and grinding efficiency to reduce production costs. For example, selecting grinding wheels with good abrasion resistance can reduce the number of replacements and increase productivity.
Environmental factors
Select appropriate grinding wheel material and grinding method according to the production environment to reduce environmental pollution.
Consider the environmental requirements of grinding wheel treatment and waste, and select grinding wheels and grinding methods that meet environmental standards.
V. Conclusion
Grinding wheel selection is a comprehensive process that requires decision-making based on the workpiece being processed, the grinding wheel abrasive, and other important factors. Through the guide in this article, readers can have a more comprehensive understanding of the key factors of grinding wheel selection, so as to make a more reasonable and accurate choice to improve processing quality and efficiency. In practice, it is also necessary to flexibly adjust the grinding wheel selection strategy according to the specific situation in order to achieve the best machining results.
Key words:
Grinding tools and abrasives
Next
Related News
Address: No. 1-6, North Road, 50 m west of the intersection of Industrial Avenue and Pingshun Road, Xiping County, Zhumadian City, Henan Province
Telephone:+8613979353005
View Mobile
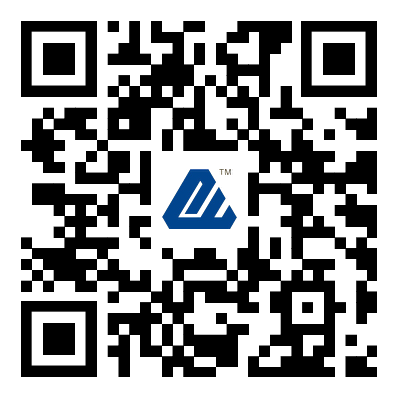