Introduction and application scenarios of resin high-power grinding wheels
Release time:
2024-06-01
Resin abrasives in solidified abrasives, also known as resin grinding wheels, are important varieties with a wide range of market
Resin abrasives in solidified abrasives, also known as resin grinding wheels, are important varieties with a wide range of market applications and market share. Resin is the binding agent in resin grinding wheels. As a binding agent of the resin including, phenolic, epoxy, polyurethane, polyvinyl alcohol, etc.; resin grinding wheel high strength, can be added to the grinding wheel to strengthen the fiber mesh, reinforcing steel and other reinforcing materials, such as cutting discs, abrasive discs, most of the resin grinding wheels are not waterproof, but can be specialized in the production of waterproof type, such as epoxy resin grinding wheels grinding finish is good, the workpiece is not easy to burn, the resin grinding wheels are applied to cutting discs, double-end, heavy duty grinding wheels, polishing wheels, and so on, resin bonding agent is an important variety of market applications. Load grinding wheels, polishing wheels, etc., the strength of resin bond grinding wheels is lower than that of metal bond and ceramic bond.
China's resin abrasives development speed is relatively fast, whether it is from the production, quality and variety of products are growing year by year, especially in recent years has formed a booming development of a good situation. Why the resin bonded abrasives will develop so fast, in addition to the objective conditions, such as social needs of large quantities, there are sufficient raw materials. The more direct and fundamental reason is that the resin bond has a unique performance is inseparable.
First, the resin grinding wheel has other grinding wheels have no advantages
(A) First of all, it is the combination of high strength. Compared with other binding agent, resin has a higher bond strength, can be used at higher speeds, can withstand greater grinding pressure, and thus in the steel and foundry industry to clean up the burr and rough grinding process is widely used. At the same time, with the improvement of the grinding process, the grinding load and strength of the cutting piece of the requirements of the higher and higher, has been developed from the past handheld grinder and suspended grinder to today's high-speed heavy-duty billet grinding machine, cutting piece of the use of the speed has been developed from the past 35-40 m / s to today's 80-100 m / s, the load of the wheel has been developed from the past 300-500N, to today's more than 10,000N, and the grinding wheel has been used in the steel and foundry industry to clean up the burr and rough grinding process. To today's more than 10,000N, if there is no high-strength binding agent is difficult to realize.
(ii) can be made into special shapes and special needs of the abrasives. This is mainly because the resin bond is hardened at low temperatures (below 200 ℃), will not change the basic properties of the material, and thus can be added in order to different needs of filler materials or reinforcing substances. For example, in order to adapt to the grinding requirements can be made with grooves and porous grinding wheels, in order to improve the strength of the grinding wheel can be added to the cutting piece of glass wire mesh cloth and other wires and so on. In order to increase the conductive properties can be added to copper powder, aluminum powder and graphite powder.
(C) suitable for the manufacture of various specifications of the sheet grinding wheel. In many metal processing departments in the cutting and grooving process has been widely used, ultra-thin can reach 0.1 mm, it completes the general saw blade can not complete the processing task, especially high-speed enhancement of the cutting blade has been widely used after the need to cut the wheel increases very quickly.
(iv) The resin bond has a certain degree of elasticity. In the grinding process, it is conducive to meeting the requirements of higher surface roughness of the workpiece. In the machining process, fine grinding and polishing process more use of resin bond grinding wheel, the same conditions for grinding, resin abrasives finish is higher than ceramic abrasives.
Second, the shortcomings of the resin grinding wheel also exists, limiting its development and application
(A) poor heat resistance. The durability of the cutting blade will be affected. Therefore, when selecting grinding wheels, the same grinding conditions, resin is harder than ceramic bond.
(ii) Poor alkali resistance. When stored in alkaline solution for a long time, the resin is easily damaged and its bond strength and hardness will gradually decrease. Therefore, in the process of grinding with resin abrasives, alkaline, especially strong alkaline coolant should be avoided as much as possible.
(iii) Resin abrasives have poor water resistance. Prolonged exposure to moisture is likely to reduce its bonding properties, so resin abrasives should not be stored for a long time, more than one year should be re-examined for strength and performance.
Three resin grinding wheel classification and characteristics
According to the abrasive material is generally divided into ordinary resin grinding wheel and super-hard resin grinding wheel.
Ordinary resin grinding wheel is white corundum, brown corundum, silicon carbide and other common abrasives as the main grinding component of the wheel, super-hard resin grinding wheel is diamond or CBN as the main grinding component of the wheel.
This article mainly introduces the resin bond ordinary grinding wheel, focusing on the cutting machine electric power greater than or equal to 5.5KW application scenarios of high-power resin cutting wheel.
Resin grinding wheels are mainly characterized by the following aspects:
1, high bond strength, such as high-speed cutting wheel using line speed up to 80-100m / s, heavy duty grinding wheel grinding load from the past about 50kg to more than 1000kg.
2, easy to adjust the structure and performance, resin abrasives hardening temperature is only about 185 ° C, much lower than the ceramic abrasives 1300 ° C firing temperature, so you can chain in the abrasives into the grid cloth, wire, graphite powder, nuts and other materials to adapt to different grinding needs. Many filler properties can still be maintained after making the abrasive, so the use of different fillers can change the performance of the abrasive in a wide range.
3, resin grinding has a certain degree of elasticity, is conducive to improving the finish of the processed workpiece, the use of graphite, chromium oxide and other polishing materials as filler can further reduce the roughness.
4, processing is not easy to burn the workpiece, resin in 230 ℃ on the gradual charring, processing of high temperature so that the resin local charring, resulting in self-sharpening, improve the sharpness of the grinding and thus reduce the grinding temperature to avoid burns on the workpiece.
5, because the resin has good molding properties, but also has good toughness, and can be made of about 0.1mm thickness of the sheet grinding wheel, used for slotting cutting.
6, resin abrasives production cycle is short, simple equipment, less investment and quick results. It is the starting product of many abrasive factories.
7, resin abrasives poor water resistance, alkali resistance, short shelf life, is its shortcomings, production and use should be noted.
8, resin abrasives used in large quantities in the manufacture of cut-off grinding wheels, cymbal grinding wheels, heavy-duty grinding wheels, roll polishing wheels, graphite mirror grinding wheels, conductive grinding wheels, honing wheels, soft polishing wheels and so on.
Four resin high-power introduction and characteristics
1 high-power cutting machine will usually use cutting machine power greater than 5.5KW, speed up to 2800 rpm.
2 universal cutting workpiece cut diameter or shape development of shaped castings and other occasions.
3 use scenarios generally require high productivity, so the wheel cutting torque force is greater, the cutting blade damage is also greater, and therefore will require the cutting blade to have a certain degree of rigidity.
For this reason, high-power resin cutting salad thickness is generally thicker, the wheel thickness is generally more than 3.4mm.
4 cutting surface temperature will be very high, so the grinding wheel itself needs to be good sharpness.
At the same time, individual factory use scenarios, in order to reduce the cutting temperature, cutting with water cooling. Experiments have proved that: if cutting with water cooling can improve the durability of the cutting blade 1.5-2 times. But some occasions do not have the conditions to add water cooling, so domestic manufacturers of high-power grinding wheels will consider the production of high-power cutting discs will be added according to the formula of the self-sharpening agent or sharpener, in order to help reduce the cutting temperature, with the service life of the cutting disc into the improvement.
5 High-power resin cutting disc application
1) Mainly used to cut cast steel, carbon steel, high carbon steel, stainless steel riser, alloy steel and other high hardness and high viscosity materials. 2) Especially suitable for precision casting industry
Five resin high-power classification
According to the factory use scene is divided into 3 categories.
1 ordinary general-purpose type: formula design bond suitable for cutting ordinary metal, cast steel parts and small stainless steel alloy castings
2 sharp type: cutting stainless steel materials with relatively high hardness, generally require cutting stainless steel pouring riser without burns.
3 durable: suitable for cutting general angle iron, steel pipe and other stainless steel metal materials; special application scenarios are suitable for cutting stainless steel solid ingot diameter 250mm.
Six resin high-power formula design and production process recommendations
With the domestic market requirements of the resin grinding wheel, high-power grinding wheel production and innovation must be based on the formulation design and the application of new materials. In this paper, only a brief introduction to the design of the formula and high-power grinding wheel manufacturing process needs to pay attention to matters.
(A) resin high-power grinding wheel common specifications
1 41-300/305×2.5/3.0×25.4/32
2 41-350/355×3.4-3.8×25.4/32
3 41-400/405×3.4~4.0×25.4/32
Resin high-power grinding wheels are generally used at a speed of 80m / s, individual occasions need 100m / s.
(II) Introduction to the basic process of resin high-power grinding wheels
1 Mixing process
A) Resin liquid: It is necessary to use high viscosity resin liquid. Zihan company's MY-0828 viscosity of 3000mPa.s or more, is a professional development for high-power cutting wheel. In the case of high-power cutting wheel formulations with high bonding agent, there is no head when mixing, and the mixture is parked for 2-3 days, still has good moisturizing properties, which is greatly beneficial to the manufacture of high-power cutting wheels.
The following two are microscope magnification of the mixing effect.
Since, most of the high power resin grinding wheels are high bonded wheels, it is necessary to find the optimal bonding agent ratio point with different application scenarios through many rounds of tests.
B) Resin Powder: It is necessary to use high fluidity gelling time short stable phenolic resin powder. Zihan's YT-0919T and YT-0919TD have obvious advantages. The flow degree is above 40mm, and the high power grinding wheel made is easy to realize that the mesh is buried inside the sand layer.
The following is a microscope of bad mixing, you can see that the mixing is not uniform, especially the auxiliary materials.
2 molding process
A) molding press: press tonnage as large as possible, generally require more than 500 tons; Zihan company's MY-0828 resin liquid as a result of mixing the material, parked for a long time to be able to moisturize, all very good solution to do high-power resin grinding wheel requires a particularly large tonnage press, even with the existing general-purpose presses, as well as the ability to do high-density high-powered grinding wheel.
B) molding holding time: according to the press tonnage to be adjusted appropriately. It is recommended that the holding time should be longer, made of high-power grinding wheel durability will be effectively guaranteed.
3 hardening process
A) the use of long hardening curve hardening: due to high-power grinding wheel, belongs to the category of high-density grinding wheels with high binding agent, so in the hardening curve setting, to use a long hardening curve. The general length of the hardening curve is more than 30 hours.
B) the use of pressure hardening: hardening must be added spring pressure hardening, so as to ensure that the molding density of high-power resin grinding wheel consistent.
C) After hardening the wheel should have a certain degree of oil: the appearance of the wheel is bright, and the abrasive particles are completely covered by the resin material. At the same time, the mesh needs to have most of it buried inside the grinding wheel layer, the best performance of the grinding wheel. ,,
Key words:
Grinding tools and abrasives
Previous
Next
Previous:
Next:
Related News
Address: No. 1-6, North Road, 50 m west of the intersection of Industrial Avenue and Pingshun Road, Xiping County, Zhumadian City, Henan Province
Telephone:+8613979353005
View Mobile
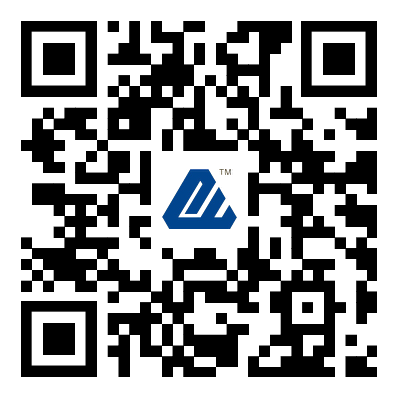